April Membership Special
3-years for $100
Just buy a Single User Membership and your $100 gets you three (3) years of access instead of one (1) year
CLICK HERE to Renew your Membership
CLICK HERE for a NEW Membership
CLICK HERE to see eligibility requirements for FREE Membership
If you have any questions, please contact me
SAFTENG has:
- Over 18,000 categorized unsafe acts/conditions and accident/injury photos
- Over 1,500 ppt's & doc's in the SAFTENG Library
- Over 4,000 Technical Articles on Process Safety, Emergency Response & OSH topics
- Over 450 videos (those not allowed on YouTube Channel)
Many THANKS to my NEW Members and those who CONTINUE to support SAFTENG:
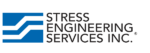
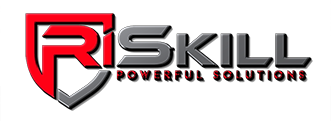
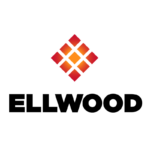
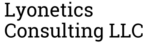
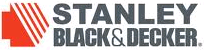
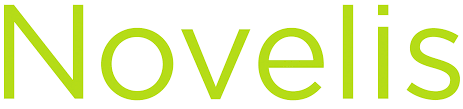

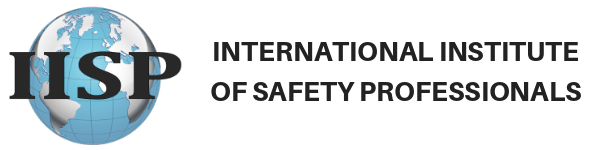
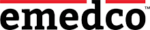



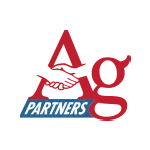

February 17, 2016
U.S. Department of LaborOccupational Safety and Health AdministrationDirectorate of Technical Support and Emergency ManagementOffice of Science and Technology Assessment Introduction Many electric power plants now use hydrogen gas-cooled electric generators versus air- or water-cooled generators. To prevent injury or fatality, employers must ensure hydrogen gas is completely purged from generator housings...
Read More
Does your PSM/RMP utilize “check valves” as a safe guard to PRVENT “reverse flow”? (NRC and API 570)
February 16, 2016
Check valves are a common piece of equipment within chemical processes; however, often times these specialized valves go years without any inspection or verification they are performing as designed. In some processes, these valves play a pivotal role in PREVENTING the initiation of an incident and can even be the sole layer of protection for the process deviation. And yet, most check valves sit in...
Read More
February 16, 2016
OSHA’s PSM and EPA’s RMP standards require the employer to develop the Process Safety Information (PSI) regarding each covered process’s “safety systems”. 1910.119(d)(3)(i) Information pertaining to the equipment in the process shall include:… 1910.119(d)(3)(i)(H) Safety systems (e.g. interlocks, detection or suppression systems). §68.65 Process safety...
Read More
February 16, 2016
So today my e-mail box overflowed with questions regarding the use of medical devices such as hearing aids, noise canceling hearing protection, and medicine pumps in HAZLOCs. And yes, there is a solution for these VERY LIMITED opportunities to use a device that is NOT certified for use in these HAZLOCs by a 3rd party NRTL. I want to be up-front with you, I am not a fan of this RAGAGEP,...
Read More
February 14, 2016
One area that we commonly find during audits and assessments is the lack of complying with the state’s fire, building and mechanical codes. Often times we find that no one involved in the project(s) were even aware of these baseline state requirements for storing and/or processing hazardous materials. Now EACH STATE is different, but this letter from the IL State Fire Marshal to businesses...
Read More
February 14, 2016
State Fire Marshal Larry L. Flowers is pleased to announce the initiation of the Ohio Department of Commerce, Division of State Fire Marshal’s (SFM) administrative rule update process for the 2011 Ohio Fire Code (OFC) and associated SFM rules (also known as Ohio Administrative Code sections 1301:7-7- 01 through 1301:7-7-47). The targeted effective date of the new OFC will be early in 2017, which...
Read More
February 13, 2016
This week during my ASSE PSM Training course I had conversations at lunch and after the course around the use of the “fitness bands” that seem to be so popular in “wellness programs” that so many companies are doing. These wellness plans have a lot of financial incentives to encourage employees to participate. Both of these organizations had such programs and the...
Read More
February 13, 2016
Bottle #1 – WRONG; “not windex” is not a label and to top it off, look at pic #2. Sure looks like Windex and it was being used like Windex, because it was Windex! All joking aside, these types of UNSAFE labeling practices are what lead to those bizarre incidents that show up in the Incident Alerts at least 3-4 times each year of people ingesting hazardous chemicals. From...
Read More
February 13, 2016
This report summarizes the results of a Campbell Institute research project to aggregate the best practices of world-class organizations in EHS around the management of contractor and supplier safety. The area of contractor safety management is especially pertinent in an increasingly global and complex world that involves work in multiple countries, non-routine work and the use of international...
Read More
February 12, 2016
OSHA initiated an inspection on Aug. 4, 2015, under its national emphasis program focused on chemical manufacturers. Inspectors found deficiencies in the employer’s equipment process safety information, process hazard analysis, written operating procedures, contractor safety, equipment inspection and testing along with management of process changes, resulting in the citations. PLEASE NOTE: this...
Read More