Let us help you make sense of PSM / RMP!
My friend Brian Chapin will be offering an open-enrollment PSM/RMP class in Burleson, Texas, July 8th to 11th, 2025. Brian is an absolute pro in NH3 Refrigeration Process Safety. Anyone who attends will also get a FREE membership to SAFTENG. You can get more information on the class with this link.
CLICK HERE to Renew your Membership
CLICK HERE for a NEW Membership
CLICK HERE to see eligibility requirements for FREE Membership
If you have any questions, please contact m
SAFTENG has:
- Over 18,000 categorized unsafe acts/conditions and accident/injury photos
- Over 1,500 ppt's & doc's in the SAFTENG Library
- Over 4,000 Technical Articles on Process Safety, Emergency Response & OSH topics
- Over 450 videos (those not allowed on YouTube Channel)
Many THANKS to my NEW Members and those who CONTINUE to support SAFTENG:
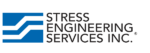
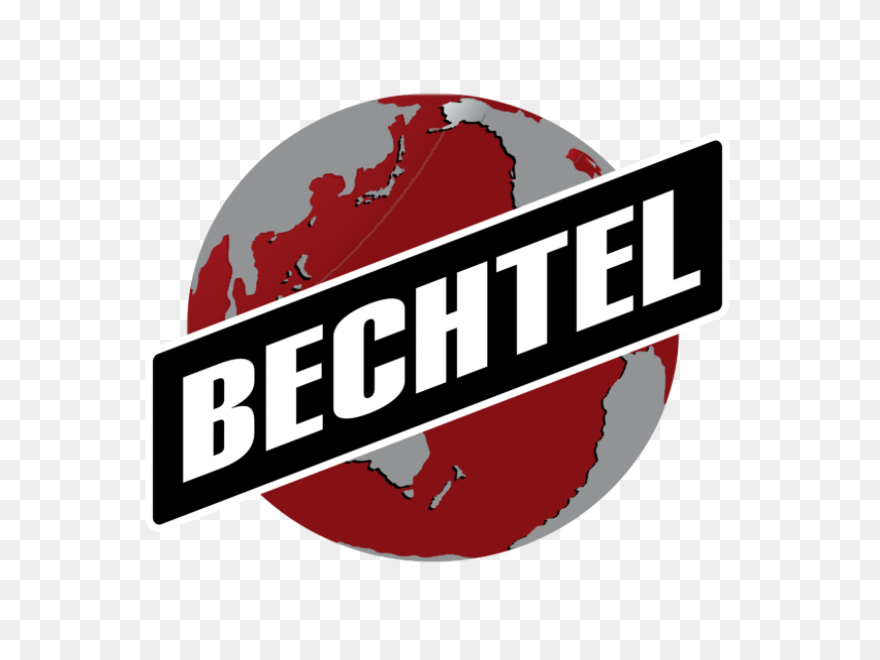
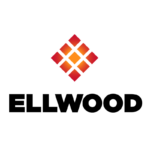
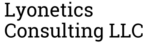
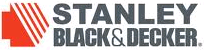
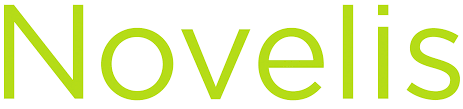

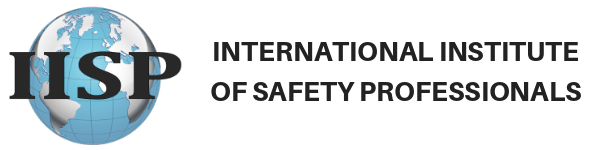
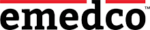


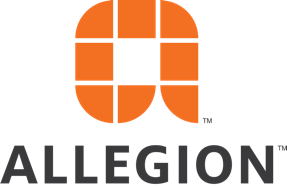
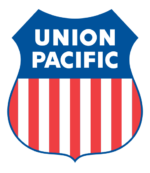
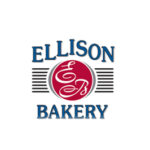
May 26, 2025
At 2:46 p.m. on September 16, 2024, Employee #1 (20) and Employee #2 (age unknown) were conducting inspections and maintenance on a tanker trailer previously used to transport propane. The tank was to be emptied using flaring, in which the remaining gas is vented through a hose to a large tripod “flare” device. The top of the flare is then ignited to burn the gas, rather than releasing...
Read More
May 26, 2025
I have scrubbed the names of the accused and deceased worker, as this could happen at just about any facility where hazardous materials are present. I should also state, the lawyers are suing the Refinery, the deceased employer (a contractor firm hired by the refinery), the manufacturer of the H2S monitor, the parent company of the manufacturer, the marketing company of the manufacture, and the rental...
Read More
May 26, 2025
Respondent owns and operates a Gas Plant. On or about July 11 and 12, 2023, representatives of the EPA inspected the Respondent’s Facility to determine compliance with Section 112(r) of the CAA and 40 C.F.R. Part 68. Information gathered during the EPA inspection revealed that Respondent had greater than 10,000 pounds of propane and greater than 10,000 pounds of flammable mixture (Butane, Ethane,...
Read More
May 23, 2025
In August 2024, while loading anhydrous ammonia into a railcar at a manufacturing site, a shear coupling on the loadout arm failed to function. Two out of three bolts failed, causing the coupling to open and resulting in a loss of primary containment (LOPC) of pressurized liquefied ammonia, which formed an ammonia vapor cloud. A proximity sensor adjacent to the shear coupling was not actuated....
Read More
May 23, 2025
All alcohols are NOT created equal! Alcohols may be flammable, but there is one alcohol whose flammability is NOT its primary hazard. Most know about ETHANOL. It is used in fuels, as well as in food and drinks. It is flammable, and its flammability is its PRIMARY HAZARD. But its sister, METHANOL, is VERY DIFFERENT. Both are flammable, but METHANOL is very toxic, making its TOXICITY its PRIMARY HAZARD....
Read More
May 23, 2025
Industrial Safety can be explained in two (2) simple aspects: 1) Culture/Management 2) Technical Safety Culture/Management is simply stated as MANAGEMENT OWNS and DRIVES safety. Without this aspect, the quality of the safety process means very little. Technical Safety is the QUALITY of the Safety Management System and its ability to meet the expectations that Management has established. Neither can...
Read More
May 22, 2025
A CSB safety video on its investigation into the fatal December 8, 2020, explosion at the Optima Belle chemical facility in Belle, West Virginia.
Read More
May 22, 2025
The chlorine (Cl2) event in TX this week has been reported as a 10,000-pound release that lasted 48 minutes. Three of the four workers injured in the incident have been released, while the fourth is still receiving treatment.
Still no word on what caused the release or what part of the primary containment system failed.
Read More
May 22, 2025
OSHA announced it has updated the inspection program that directs agency enforcement resources to establishments with the highest rates of injuries and illnesses based on injury and illness data submitted in accordance with OSHA’s recordkeeping requirements. The Site-Specific Targeting program is OSHA’s primary planned inspection program for non-construction establishments with 20 or...
Read More
May 21, 2025
At 12:30 p.m. on February 7, 2022, an employee, 45, was disconnecting the discharge line of a 4-inch mobile water pump. The discharge line was blocked with ice, and the running pump was deadheaded, leading to a buildup of heat and pressure in the discharge line after the check valve.
…
HomeRead More »
Read More
May 21, 2025
Another tragic ending to a “Line Break” gone bad. This one involved opening a flange on a steam line in an attempt to “bleed off” the steam by loosening flange bolts. IT DID NOT GO AS PLANNED, and two workers perished with 70% burns! At 6:52 p.m. on August 10, 2020, two (2) employees (30) and a coworker were attempting to remove a blockage from a hydrolyzer. The employees and...
Read More
May 21, 2025
As we have discussed here for years, “flanged joints” are usually MORE difficult to manage than are welded connections. However, somehow the rumor got started that flanged connections can be done by “Billy Joe Jim Bob.” Nothing could be further from the truth! And guess which connections most often leak? Yep, flanged connections. There are many reasons for this higher leak rate,...
Read More