Let us help you make sense of PSM / RMP!Â
My friend Brian Chapin will be offering an open-enrollment PSM/RMP class in Burleson, Texas, July 8th to 11th, 2025. Brian is an absolute pro in NH3 Refrigeration Process Safety. Anyone who attends will also get a FREE membership to SAFTENG. You can get more information on the class with this link.Â
CLICK HERE to Renew your Membership
CLICK HERE for a NEW Membership
CLICK HERE to see eligibility requirements for FREE Membership
If you have any questions, please contact m
SAFTENG has:
- Over 18,000 categorized unsafe acts/conditions and accident/injury photos
- Over 1,500 ppt's & doc's in the SAFTENG Library
- Over 4,000 Technical Articles on Process Safety, Emergency Response & OSH topics
- Over 450 videos (those not allowed on YouTube Channel)
Many THANKS to my NEW Members and those who CONTINUE to support SAFTENG:
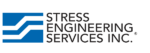
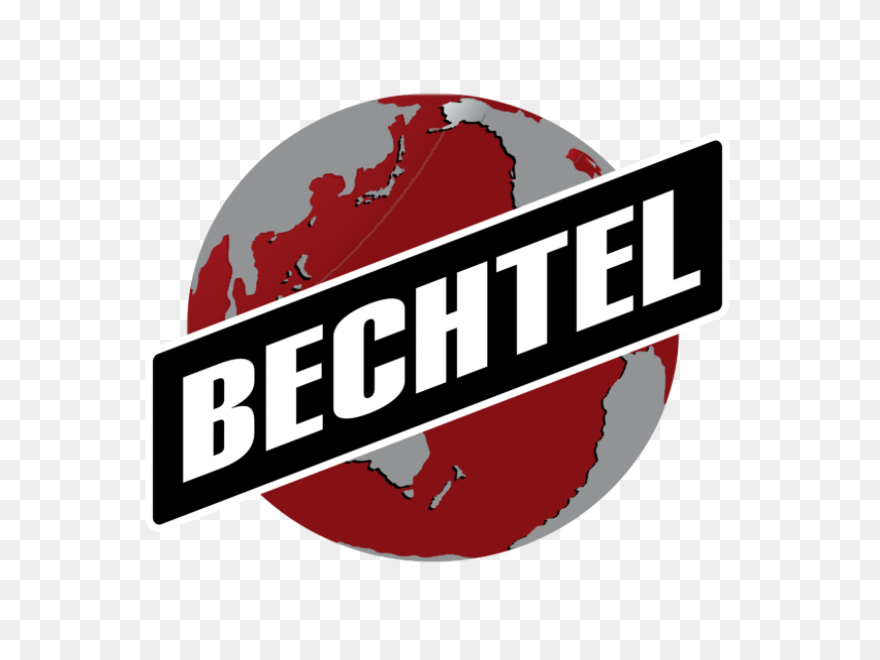
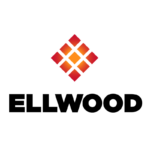
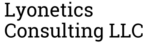
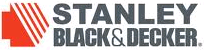
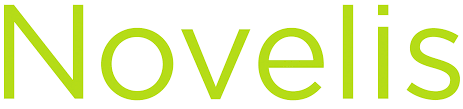

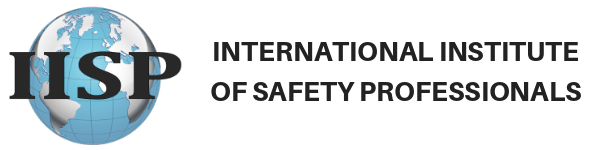
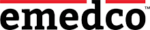


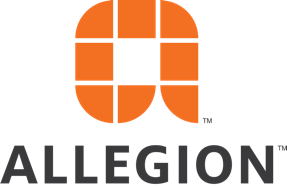
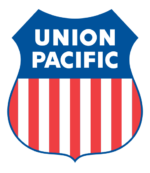
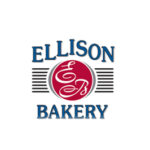
March 26, 2011
ERPs are based on site-specific needs and experience. It is important to consider previous emergency incidents in preparing an ERP. It is just as important to consider new information, experience, and incidents with the goal of enhancing the effectiveness of the ERP and keeping it current. Written procedures for the critique of an emergency response must be part of the ERP. Appropriate changes should...
Read More
March 26, 2011
The plan must also address how employees will be informed that an emergency exists and how they should respond. The alarm system must inform “all affected employees” that an emergency exists and what their immediate response should be based on the alarm sequence. There are three important questions that need to be addressed:(a) Who needs to be made aware of the emergency?(b) What do they...
Read More
March 26, 2011
The plan must provide for advanced first aid support trained personnel. These personnel must be qualified Basic Life Support (BLS) personnel or better-trained personnel. BLS refers to a unique group of trained individuals (e.g., EMTs) who have received an established level of specialized training that exceeds basic first aid skills such as control of bleeding and cardiopulmonary resuscitation (CPR)....
Read More
March 26, 2011
The ERP must contain provisions for decontamination of emergency responders leaving the exclusion zone. Individuals who will assist the responders as they leave the exclusion area must be trained in decontamination procedures. These individuals must wear PPE at the same level or one level below that worn by the emergency responders they are supporting, as appropriate to the hazards. Decontamination...
Read More
March 26, 2011
All employees that are not trained in emergency response and who will not be needed during the response operation should be evacuated from the exclusion and decontamination zones. This aspect of the ERP should be in compliance with 1910.38 as described in Section XII.A.2. CSHOs must use 1910.38 as a model to evaluate the employer’s “evacuation routes and procedures.” The CSHO shall...
Read More
March 26, 2011
Areas surrounding the danger area must be controlled during emergencies by prohibiting unauthorized personnel from entering the emergency release area. Methods of excluding areas and defining various zones need to be addressed in the ERP.
…
HomeRead More »
Read More
March 26, 2011
Safe places of refuge (out-of-doors or shelter-in-place) should be the areas where an accounting of all employees will be performed. This can be critically important for identifying individuals who did not get out, estimating where they may be, and initiating any rescue operation. Information on safe places of refuge must be given to the emergency response organization or emergency response team promptly....
Read More
March 26, 2011
This is by FAR the most misunderstood element of all!
The ERP must define the types of releases that could potentially require an emergency response and should define what types of releases would not be an emergency, or, in other words, what may be handled as an “incidental release.”
…
HomeRead More »
Read More
March 26, 2011
Personnel roles must be clearly defined in the ERP. One method of doing this is to list job titles and describe their projected roles in emergency response operations. Although specific HAZWOPER titles are not required, employees should be designated to assume duties that parallel 1910.120(q)(6) and must be trained accordingly.
…
HomeRead More »
Read More
March 26, 2011
We see a lot of great efforts on emergency response plans, but so many times, folks do not know the details OSHA will be looking for. Here are the required sections/information for your ERP and the details required.
(q)(2)(i) Pre-emergency Planning and Coordination
…
HomeRead More »
Read More
March 26, 2011
Most of the facilities we work at have a mechanical integrity program for the process equipment. Most have a Work Order system for their preventative maintenance program. This system kicks out a work order for the PM(s) due. Most facilities track the closure rates of the PM W.O.’s. My tip… Add ALL of your emergency response equipment to this system. Items such as: sprinkler annual flow...
Read More
March 26, 2011
That is PSM lingo for…when you are utilizing Risk Based Inspection (RBI) protocols and you wish to extend the inspection or PM frequencies on a piece of covered equipment, this is without a doubt a change that REQUIRES an MOC.
…
HomeRead More »
Read More